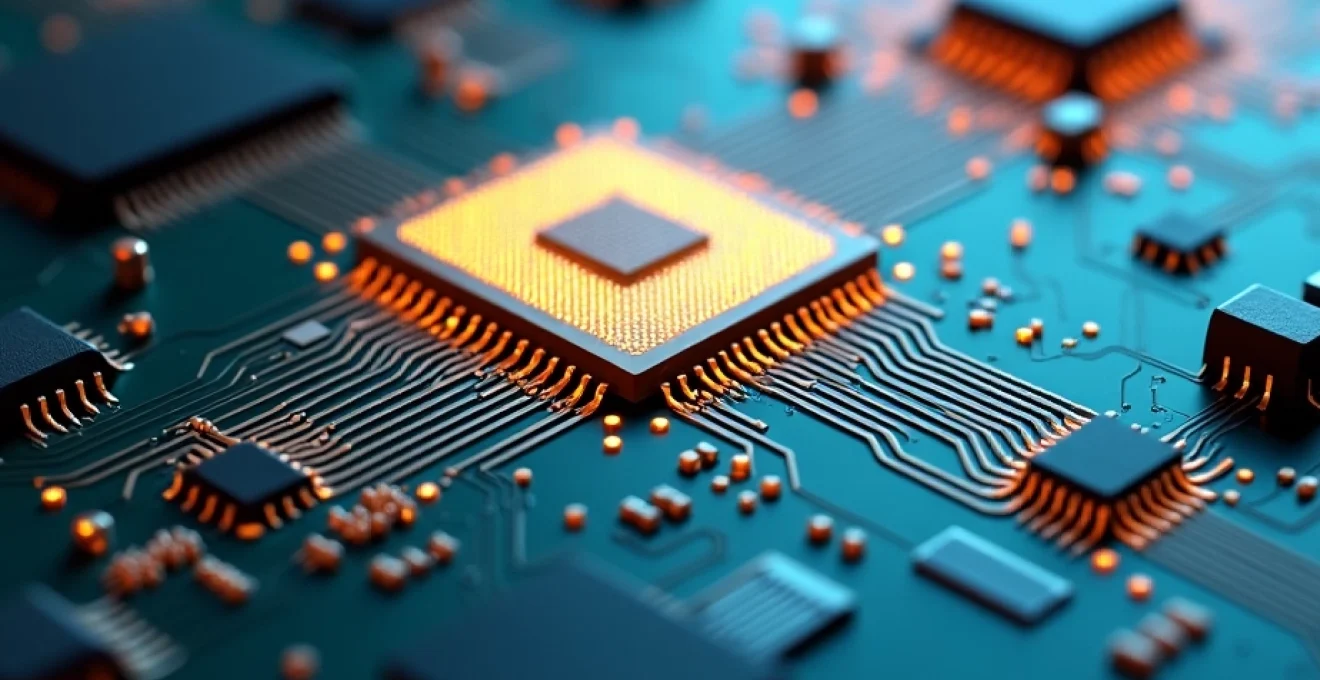
High-Density Interconnect (HDI) Leiterplatten repräsentieren einen bedeutenden Fortschritt in der Elektronikfertigung. Sie ermöglichen eine deutlich höhere Packungsdichte und Leistungsfähigkeit als herkömmliche Leiterplatten. Durch ihre einzigartige Struktur und fortschrittliche Fertigungstechnologien bieten HDI-PCBs zahlreiche Vorteile für moderne elektronische Geräte. Insbesondere in Bereichen, wo Miniaturisierung und hohe Leistung gefragt sind, setzen sich HDI-Leiterplatten zunehmend durch. Doch was genau macht diese Technologie so besonders? Welche konkreten Unterschiede bestehen zu Standard-PCBs?
Technologie und Struktur von HDI-Leiterplatten
Die Technologie und Struktur von HDI-Leiterplatten unterscheiden sich grundlegend von herkömmlichen PCBs. Während Standard-Leiterplatten oft mit relativ großen Durchkontaktierungen und breiten Leiterbahnen arbeiten, setzen HDI-Boards auf deutlich feinere Strukturen. Dies ermöglicht eine viel kompaktere Bauweise bei gleichzeitig höherer Funktionalität. Ein Schlüsselelement sind dabei die sogenannten Mikrovias - winzige Verbindungen zwischen den Lagen.
Mikrovia-Technologie in HDI-PCBs
Mikrovias sind das Herzstück der HDI-Technologie. Diese extrem kleinen Durchkontaktierungen, oft mit einem Durchmesser von weniger als 150 Mikrometern, ermöglichen eine viel dichtere Verdrahtung als bei herkömmlichen PCBs. Sie können als blinde, vergrabene oder gestapelte Vias ausgeführt werden. Durch ihre geringe Größe lassen sich auf der gleichen Fläche deutlich mehr elektrische Verbindungen realisieren. Dies ist besonders wichtig für hochintegrierte Schaltungen mit einer Vielzahl von Anschlüssen.
Lagenaufbau und Stackup-Design bei HDI
HDI-Leiterplatten zeichnen sich durch einen komplexeren Lagenaufbau aus. Während Standard-PCBs oft mit 4-6 Lagen auskommen, können HDI-Boards problemlos 10 oder mehr Lagen enthalten. Der Stackup - also die Anordnung und Verbindung dieser Lagen - ist dabei entscheidend für die Leistungsfähigkeit. Durch geschicktes Design lassen sich Signalwege optimieren und Störeinflüsse minimieren. Ein typischer HDI-Stackup könnte beispielsweise aus mehreren Signallagen bestehen, die durch dünne dielektrische Schichten und Masse-/Versorgungslagen getrennt sind.
Kupferkaschierung und Leiterbahnbreiten
Bei HDI-Leiterplatten kommen deutlich dünnere Kupferkaschierungen zum Einsatz als bei Standard-PCBs. Typischerweise werden Dicken von 17 μm oder weniger verwendet, verglichen mit 35 μm oder mehr bei herkömmlichen Boards. Dies ermöglicht feinere Leiterbahnstrukturen. Die Leiterbahnbreiten und -abstände können bei HDI-Designs auf 75 μm oder weniger reduziert werden. Zum Vergleich: Bei Standard-PCBs liegen diese Werte oft bei 100 μm oder darüber. Diese Miniaturisierung ist ein Schlüsselfaktor für die hohe Packungsdichte von HDI-Leiterplatten.
Laser-Bohrverfahren für HDI-Strukturen
Ein entscheidender technologischer Unterschied liegt im Bohrverfahren. Während bei herkömmlichen PCBs mechanische Bohrungen dominieren, kommen bei HDI-Boards präzise Laser zum Einsatz. Diese ermöglichen die Herstellung der winzigen Mikrovias mit höchster Genauigkeit. Lasergebohrte Vias können Durchmesser von unter 100 μm erreichen - eine Präzision, die mit mechanischen Verfahren nicht möglich wäre. Zudem erlaubt die Lasertechnologie eine flexible Positionierung der Vias, was dem Entwickler mehr Freiheiten beim Layout gibt.
Die Laser-Bohrtechnologie revolutioniert die Leiterplattenfertigung und ermöglicht Strukturen, die vor wenigen Jahren noch undenkbar waren.
Fertigungsprozesse für HDI-Leiterplatten
Die Herstellung von HDI-Leiterplatten erfordert spezialisierte Fertigungsprozesse, die sich deutlich von der Produktion herkömmlicher PCBs unterscheiden. Diese fortschrittlichen Verfahren ermöglichen die Realisierung der komplexen Strukturen und feinen Details, die für HDI-Designs charakteristisch sind. Besonders hervorzuheben sind dabei die sequenzielle Laminierung, hochpräzise fotolithografische Prozesse und spezielle Oberflächenbehandlungen.
Sequential Lamination bei HDI-Herstellung
Ein Kernmerkmal der HDI-Fertigung ist die sequenzielle Laminierung. Im Gegensatz zur einmaligen Laminierung bei Standard-PCBs werden HDI-Boards in mehreren Schritten aufgebaut. Dabei werden zunächst die inneren Lagen mit Mikrovias hergestellt und laminiert. Anschließend werden weitere Lagen hinzugefügt, wobei jede neue Lage ihre eigenen Mikrovias erhält. Dieser Prozess ermöglicht die Realisierung komplexer 3D-Strukturen innerhalb der Leiterplatte. Die sequenzielle Laminierung ist entscheidend für die Herstellung von gestapelten und versetzten Vias, die charakteristisch für fortschrittliche HDI-Designs sind.
Fotolithografische Prozesse für Feinstrukturen
Die Erzeugung der feinen Leiterbahnstrukturen in HDI-Leiterplatten erfordert hochpräzise fotolithografische Prozesse. Dabei kommen spezielle Fotoresiste und Belichtungsverfahren zum Einsatz, die eine deutlich höhere Auflösung ermöglichen als bei Standard-PCBs. Die Verwendung von Laser Direct Imaging (LDI) ist besonders verbreitet, da es eine exakte Übertragung des Designs auf die Leiterplatte erlaubt. Diese Technologie ermöglicht Leiterbahnbreiten und -abstände von unter 50 μm, was für die hohe Packungsdichte von HDI-Boards essentiell ist.
Oberflächenbehandlung und Finishing-Optionen
Die Oberflächenbehandlung spielt bei HDI-Leiterplatten eine noch wichtigere Rolle als bei herkömmlichen PCBs. Aufgrund der feinen Strukturen und der oft höheren elektrischen Anforderungen kommen spezielle Finishing-Verfahren zum Einsatz. Beliebte Optionen sind ENIG (Electroless Nickel Immersion Gold) oder ENEPIG (Electroless Nickel Electroless Palladium Immersion Gold) . Diese Verfahren bieten exzellente Lötbarkeit und Korrosionsschutz bei gleichzeitig geringer Schichtdicke, was für die feinen HDI-Strukturen ideal ist. Zudem werden oft selektive Oberflächenbehandlungen eingesetzt, um unterschiedliche Bereiche der Leiterplatte optimal für ihre jeweilige Funktion zu präparieren.
Die Komplexität dieser Fertigungsprozesse macht die Produktion von HDI-Leiterplatten anspruchsvoller und kostenintensiver als die herkömmlicher PCBs. Dennoch sind diese Verfahren unerlässlich, um die Vorteile der HDI-Technologie voll auszuschöpfen. Bei der Wahl eines geeigneten Herstellers für HDI-Projekte ist es wichtig, auf entsprechende Expertise und moderne Fertigungsanlagen zu achten. Erfahrene Anbieter wie https://www.icape-group.com/ verfügen über das notwendige Know-how und die technologischen Möglichkeiten, um selbst anspruchsvollste HDI-Designs zuverlässig zu realisieren.
Leistungsmerkmale von HDI-PCBs
Die einzigartigen Technologien und Fertigungsprozesse von HDI-Leiterplatten resultieren in spezifischen Leistungsmerkmalen, die sie deutlich von Standard-PCBs abheben. Diese Eigenschaften machen HDI-Boards besonders attraktiv für Anwendungen, die höchste elektrische Performance, miniaturisierte Designs und effizientes Wärmemanagement erfordern.
Signalintegrität und Impedanzkontrolle
Ein herausragendes Merkmal von HDI-Leiterplatten ist ihre überlegene Signalintegrität. Durch die kürzeren Signalwege und die Möglichkeit, Impedanzen präziser zu kontrollieren, können HDI-Boards deutlich höhere Signalgeschwindigkeiten und -qualitäten erreichen als herkömmliche PCBs. Die feinen Leiterbahnstrukturen und die Verwendung von Mikrovias reduzieren parasitäre Effekte wie Kapazitäten und Induktivitäten. Dies ist besonders wichtig für Hochfrequenzanwendungen oder schnelle digitale Schaltungen, wo jede Picosekunde zählt.
Die verbesserte Impedanzkontrolle in HDI-Designs ermöglicht zudem eine präzisere Anpassung an die Anforderungen moderner ICs. Typischerweise können Impedanztoleranzen von ±5% oder besser erreicht werden, verglichen mit ±10% bei Standard-PCBs. Dies trägt wesentlich zur Reduzierung von Signalreflexionen und -verzerrungen bei, was die Gesamtperformance des Systems steigert.
Wärmemanagement in HDI-Designs
Trotz - oder gerade wegen - ihrer kompakten Bauweise bieten HDI-Leiterplatten oft Vorteile beim Wärmemanagement. Die Möglichkeit, mehr Kupferlagen auf engem Raum zu integrieren, erhöht die thermische Leitfähigkeit der Platine. Zudem können thermische Vias strategisch platziert werden, um Wärme effizient von kritischen Komponenten abzuleiten. In Kombination mit modernen Kühlkonzepten wie eingebetteten Heatpipes oder Flüssigkeitskühlung ermöglicht dies die Realisierung hochleistungsfähiger Designs bei gleichzeitig kompakter Bauweise.
Effizientes Wärmemanagement ist der Schlüssel zur Leistungssteigerung in kompakten elektronischen Systemen.
Miniaturisierung und Komponentendichte
Die vielleicht offensichtlichste Stärke von HDI-Leiterplatten liegt in ihrer Fähigkeit zur extremen Miniaturisierung. Durch die Verwendung von Mikrovias und ultradünnen Leiterbahnen können HDI-Designs eine Komponentendichte erreichen, die mit herkömmlichen PCBs nicht möglich wäre. Es ist nicht ungewöhnlich, dass ein HDI-Board die Funktionalität mehrerer Standard-Leiterplatten auf einer deutlich kleineren Fläche vereint.
Diese hohe Packungsdichte ermöglicht nicht nur kompaktere Geräte, sondern kann auch die elektrische Performance verbessern. Kürzere Signalwege zwischen Komponenten reduzieren Laufzeitverzögerungen und elektromagnetische Interferenzen. Zudem erlaubt die HDI-Technologie eine flexiblere Platzierung von Komponenten, was dem Designer mehr Freiheiten bei der Optimierung des Layouts gibt.
Merkmal | Standard-PCB | HDI-PCB |
---|---|---|
Minimale Leiterbahnbreite | 100 μm | < 75 μm |
Via-Durchmesser | > 300 μm | < 150 μm |
Lagenanzahl (typisch) | 4-6 | 10+ |
Impedanzkontrolle | ±10% | ±5% |
Diese Leistungsmerkmale machen HDI-Leiterplatten zur bevorzugten Wahl für eine Vielzahl moderner elektronischer Produkte, insbesondere dort, wo hohe Performance auf kleinstem Raum gefordert ist. Von Smartphones über medizinische Implantate bis hin zu Automotive-Elektronik - HDI-Technologie ermöglicht Innovationen, die mit herkömmlichen PCBs nicht realisierbar wären.
Anwendungsbereiche für HDI-Leiterplatten
Die einzigartigen Eigenschaften von HDI-Leiterplatten machen sie zu einer idealen Lösung für eine Vielzahl moderner elektronischer Anwendungen. Insbesondere in Bereichen, wo Miniaturisierung, hohe Leistungsdichte und zuverlässige Signalübertragung gefragt sind, setzen sich HDI-Boards zunehmend durch. Betrachten wir einige der wichtigsten Einsatzgebiete genauer.
HDI in Smartphones und Wearables
Der Bereich der mobilen Endgeräte ist ein Paradebeispiel für den Einsatz von HDI-Technologie. Moderne Smartphones packen eine enorme Funktionalität auf kleinstem Raum. Hier sind die Vorteile von HDI-Leiterplatten besonders deutlich:
- Extreme Miniaturisierung ermöglicht dünnere und leichtere Geräte
- Hohe Signalintegrität unterstützt schnelle Prozessoren und 5G-Konnektivität
Auch im Bereich der Wearables wie Smartwatches oder Fitness-Tracker sind HDI-Leiterplatten unverzichtbar. Die extrem kompakten Gehäuse dieser Geräte erfordern eine Miniaturisierung, die nur mit HDI-Technologie realisierbar ist. Zudem ermöglicht die verbesserte Signalintegrität eine zuverlässige Datenübertragung bei minimalem Energieverbrauch - ein kritischer Faktor für die Akkulaufzeit tragbarer Geräte.
Einsatz in der Automobilelektronik
Die Automobilindustrie erlebt derzeit einen technologischen Wandel, bei dem Elektronik eine immer größere Rolle spielt. HDI-Leiterplatten sind ein Schlüsselelement dieser Entwicklung:
- Advanced Driver Assistance Systems (ADAS) benötigen hochintegrierte Sensoren und Steuergeräte
- Infotainment-Systeme erfordern kompakte Designs bei hoher Signalqualität
- Elektrofahrzeuge profitieren von der verbesserten Wärmeableitung in Batteriemanagementsystemen
Die robusten Eigenschaften von HDI-Boards machen sie besonders geeignet für die anspruchsvollen Umgebungsbedingungen in Fahrzeugen. Temperaturwechsel, Vibrationen und elektromagnetische Interferenzen stellen hohe Anforderungen an die Zuverlässigkeit, die HDI-Leiterplatten erfüllen können.
HDI-PCBs in medizinischen Geräten
Im medizintechnischen Bereich ermöglichen HDI-Leiterplatten Innovationen, die das Potenzial haben, Leben zu retten und die Patientenversorgung zu revolutionieren:
- Implantierbare medizinische Geräte profitieren von der extremen Miniaturisierung
- Bildgebende Systeme nutzen die verbesserte Signalintegrität für höhere Auflösungen
- Tragbare Diagnose- und Überwachungsgeräte werden durch HDI kompakter und leistungsfähiger
Die Fähigkeit von HDI-Boards, komplexe Funktionen auf kleinstem Raum zu integrieren, eröffnet neue Möglichkeiten für minimalinvasive Therapien und kontinuierliches Gesundheitsmonitoring. Gleichzeitig stellen die strengen Regularien im Medizinbereich hohe Anforderungen an die Zuverlässigkeit und Langlebigkeit der eingesetzten Komponenten - Kriterien, die HDI-Leiterplatten erfüllen können.
Wirtschaftliche Aspekte von HDI vs. Standard-PCBs
Die Entscheidung zwischen HDI- und Standard-Leiterplatten ist nicht nur eine technische, sondern auch eine wirtschaftliche Frage. Während HDI-Boards in der Herstellung komplexer und oft kostenintensiver sind, können sie in vielen Anwendungen langfristig die effizientere Lösung darstellen.
Kostenanalyse der HDI-Fertigung
Die Produktion von HDI-Leiterplatten ist in der Regel teurer als die herkömmlicher PCBs. Gründe dafür sind:
- Höhere Materialkosten für spezielle Substrate und Kupferfolien
- Komplexere Fertigungsprozesse wie sequenzielle Laminierung und Laser-Bohrungen
- Strengere Qualitätskontrollen aufgrund der feineren Strukturen
Dennoch kann sich die Investition in HDI-Technologie auszahlen. Durch die Möglichkeit, mehr Funktionen auf kleinerem Raum zu integrieren, können oft mehrere Standard-PCBs durch eine einzige HDI-Platine ersetzt werden. Dies kann die Gesamtkosten des Systems reduzieren und gleichzeitig die Zuverlässigkeit erhöhen.
Langzeitperformance und Zuverlässigkeit
Ein wichtiger wirtschaftlicher Faktor ist die Langzeitperformance von HDI-Leiterplatten. Durch ihre robuste Konstruktion und die Verwendung hochwertiger Materialien weisen HDI-Boards oft eine höhere Zuverlässigkeit und längere Lebensdauer auf als Standard-PCBs. Dies kann sich besonders in anspruchsvollen Umgebungen wie der Automobilindustrie oder in medizinischen Anwendungen auszahlen.
Zudem ermöglicht die verbesserte Signalintegrität von HDI-Designs oft eine höhere Systemperformance bei gleichzeitig geringerem Energieverbrauch. Langfristig kann dies zu Kosteneinsparungen im Betrieb führen, insbesondere bei batteriebetriebenen Geräten.
ROI-Betrachtung bei HDI-Implementierung
Bei der Entscheidung für oder gegen HDI-Leiterplatten ist eine ganzheitliche Return-on-Investment (ROI) Betrachtung entscheidend. Folgende Faktoren sollten dabei berücksichtigt werden:
- Reduzierung der Gesamtsystemkosten durch Integration mehrerer Funktionen
- Potenzielle Marktvorteile durch kompaktere oder leistungsfähigere Produkte
- Verringerung von Wartungs- und Ausfallkosten durch höhere Zuverlässigkeit
- Mögliche Energieeinsparungen im Betrieb
In vielen Fällen kann der anfängliche Mehraufwand für HDI-Technologie durch diese langfristigen Vorteile mehr als aufgewogen werden. Besonders in Märkten, wo Miniaturisierung und hohe Performance entscheidende Wettbewerbsfaktoren sind, kann die Investition in HDI-Leiterplatten einen signifikanten Wettbewerbsvorteil darstellen.
Die Entscheidung für HDI-Technologie sollte nicht nur auf Basis der initialen Kosten, sondern unter Berücksichtigung des gesamten Produktlebenszyklus getroffen werden.
Zusammenfassend lässt sich sagen, dass HDI-Leiterplatten zwar in der Herstellung oft teurer sind als Standard-PCBs, aber durch ihre einzigartigen Eigenschaften in vielen Anwendungen die wirtschaftlich sinnvollere Wahl darstellen können. Eine sorgfältige Analyse der spezifischen Anforderungen und Rahmenbedingungen ist entscheidend, um das volle Potenzial dieser Technologie auszuschöpfen und einen optimalen ROI zu erzielen.